FAQs
Our mission is to improve public health. Here are answers to the most frequently asked questions.
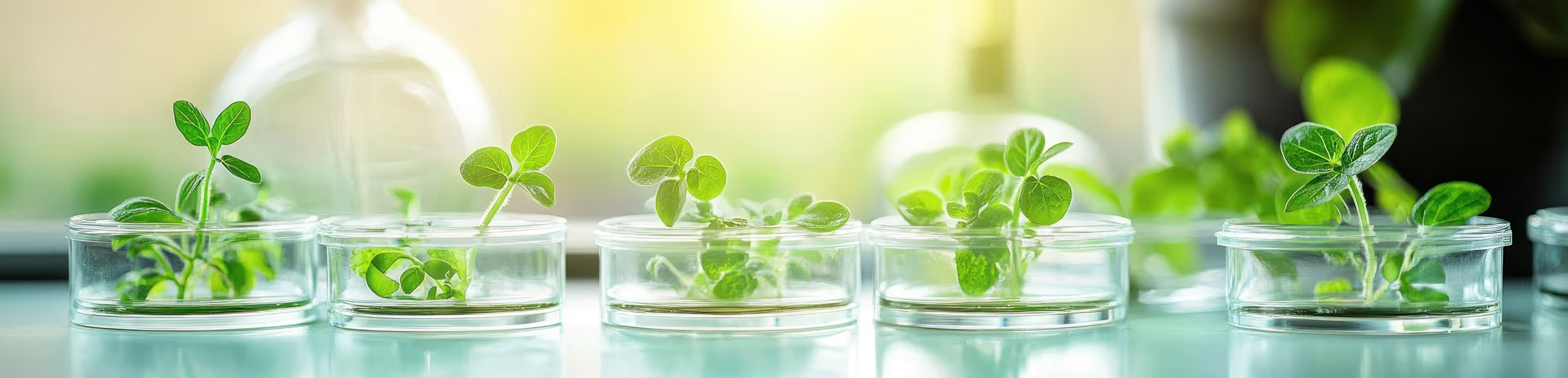
List of frequently asked questions
Hygiene and environment management services
The average number of insects caught per day per trap at our company is the standard value for insect control in floor-standing traps at pharmaceutical storage facilities
Storage area: 0.5 individuals
Box packing / inspection area: 0.15 pieces
We recommend it.
For example, if the trap installation period is 30 days
Storage area: 15 individuals / trap
Box packing / inspection area: 5 individuals/trap
is the standard value.
The JGSP “Code of Practice Concerning Quality Control and Safety Management in the Supply of Pharmaceuticals” indicates that insect phase surveys in pharmaceutical storage areas are 2 times / year. (As for the survey period, June and October, which are the periods when insects increase each year, are preferred.) However, in recent years, as requirements for the quality of pharmaceuticals have become stricter, the number of logistics warehouses that are carried out every month from the viewpoint of continuous monitoring is increasing.
In pharmaceutical manufacturing plants, of course, we consider the GMP area to be part of the pharmaceutical manufacturing environment, even if it is a non-GMP area. In order to ensure the high quality of products, it is necessary to carry out manufacturing process validation and manage the entire manufacturing environment (adoption of sanitary design, implementation of sanitation, etc.), including hygiene management of work staff. Pharmaceutical manufacturing environments are constantly exposed to the risk of contamination to products, as there is a possibility that a wide variety of microorganisms can invade (mix in) into the manufacturing work environment via people, goods, invasive animals and insects, outside air, rainwater, etc.
In order to prevent the risk of such contamination, cleaning management (cleaning validation) is essential to accurately grasp the process validation of the manufacturing environment, implement effective microbial countermeasures, and maintain a good state (conforms to the set quality control standards) at all times. Our cleaning management begins with hygiene education for work staff, and we implement and thoroughly implement all measures (measures) deemed necessary for hygiene, such as selecting and managing cleaning tools, organizing and organizing manufacturing sites, and cleaning, sterilization / disinfection, mold prevention, etc.
The person responsible for site management is dispatched from among regular employees at the head office, and work staff hired locally perform cleaning management work. The head office quality control team regularly checks work results (= cleaning quality), and if they do not meet quality control standards, they instruct and guide staff to improve work procedures, etc.
Based on our GMP compliant cleaning system standards, we will prepare procedures according to the characteristics and management concept of the facility. Our quality control is based on “work standards,” “education and training standards,” and “quality control standards,” and each standard consists of plans, procedures, and materials, and we check whether the standards and procedures were operated as planned with inspection tables, daily reports, and monthly reports, respectively. Also, when corrections are necessary, they are recorded with improvement instructions and improvement reports.
It consists of the general management department, sales, operations, and general affairs and personnel departments, and 5 senior personnel personnel are in charge. It depends on the scale of the business, but at the time of implementation, several people in charge of quality control will be assigned and the launch port will be carried out.
The work policy is considered from two aspects (microbiological aspect and actual work side), since “maintaining the hygiene of the manufacturing environment in a good state at all times” and “preventing microbial contamination.” From a microbiological perspective, the three principles of sterility are the practice of “① do not bring in bacteria ② do not spread bacteria ③ do not proliferate.” Implementation of the three requirements “① complete structural construction ② enhancement of environmental hygiene management methods ③ education / training and management of work staff” for implementing the three principles of sterility from an actual work perspective. In particular, we believe that it is important to establish cleaning and cleaning methods and constantly monitor the evaluation of results, and we carry out regular checks on work results.
Specific initiatives are as follows.
- ① Conduct detailed meetings with your staff and our work staff, and carry out hygiene management with all staff involved in the manufacturing environment
- ② Education and training on hygiene management for work staff and selection and management of cleaning tools
- ③ Quantitative and qualitative evaluation of work results based on work reports
- ④ By introducing material systems as cleaning management technology, work efficiency and productivity are increased, and environmental impact on the facility is reduced
It's not just cleaning; it's about cleaning to prevent infection. We will endeavor to improve the environment of medical facilities so that patients can live treatment and hospitalization with peace of mind, and so that health care workers can concentrate on nursing and treatment.
To that end,
- Implementation of education on hospitality manners and personal information protection
- Standard precautionary measures education
- Education on cleaning methods to prevent healthcare-related infections
We are doing it.
It is a specialist who constructs and manages environmental infrastructure by learning expertise and techniques such as medical waste handling, microbiology, sanitary design / equipment and air conditioning, plague control, cleaning technology, infection prevention measures, etc. from creating medical environment improvement systems.
It's about working to prevent infection throughout the hospital, including us. Even if some people take measures, it will not prevent infection. If even one person takes the wrong measures, the expected effect will not increase. We are taking measures from a cleaning standpoint, and by regularly holding meetings with health care workers, we are working in unity with hospitals to prevent infection.
We are taking the following infection prevention measures.
- ① Acquiring knowledge about infections
- Infection route standard prevention measures and prevention measures by infection route
- Measures related to needlestick accidents
- Handling infectious waste
- Handling PPE (personal protective equipment)
- ② Learn how to clean and disinfect blood, body fluids, filth, etc.
- ③ Hygiene management of cleaning tools
There is no problem if you request each service individually. We will prepare and propose business details in response to the hospital's requests. Of course, by including all services, hospital facilities can be managed efficiently and comprehensively.
Environmental Measurement / Analysis Service
Work environment measurement
Section 65 (1) of the Occupational Safety and Health Act states that “businesses must perform necessary work environment measurements and record the results for those stipulated by government ordinance at indoor workplaces or other workplaces where harmful work is carried out.”
I'm afraid I can't say it unequivocally, but the price varies depending on the material to be measured, the size and number of workplaces, and the location of the site. If you contact us, we will prepare a quote based on the conditions you have received.
Measurements are performed when the target work is carried out as usual. We also carry out in-house safety education, and don't worry, we are taking the utmost care so as not to interfere with work.
Air environment measurement
It is a building with an area of 3,000 square meters or more used for offices, stores, inns, box office halls, department stores, assembly halls, playgrounds, libraries, museums, art galleries, schools, training centers, etc.
In section 4 (1) of the Act on Ensuring a Hygienic Environment in Buildings, it is stated that “the specific building must be maintained and managed in accordance with the standards stipulated by government ordinance.”
I'm afraid I can't say it unequivocally, but the price varies depending on the size of the building to be measured and the location of the site. If you contact us, we will prepare a quote based on the conditions you have received.
Measurements are performed when the target building is operating as usual. Measurements are performed once in the morning and once in the afternoon at each measurement point.
Asbestos survey / analysis / measurement
I'd like to ask. However, there is a possibility that aerial work (work above the height that can be reached with a 6-foot stepladder) and complete restoration of sample collection marks (simple repairs are possible) are not compatible, so please inquire in advance.
The preliminary investigation requires a written survey using design documents, etc. before the on-site visual survey, so please prepare design documents, completion documents, and renovation work history, etc. of the building to be investigated.
It depends on how crowded the analysis is at the time of request and the number of specimens requested, but if it is up to 5 specimens, we can let you know the analysis results (preliminary report) in about 10 days. If the number of samples requested increases, please inquire in advance about the analysis delivery date.
There are 6 types: chrysotile, amosite, crocidolite, anthophyllite, actinolite, and tremolite.
It cannot be treated as undetected. According to a notification issued by the Ministry of Health, Labor, and Welfare in 2008/2, “the remaining items (anthophyllite, actinolite, tremolite) must be analyzed by going back to past measurements.”
Contact
Please feel free to contact us if you have any problems with improving the environment.
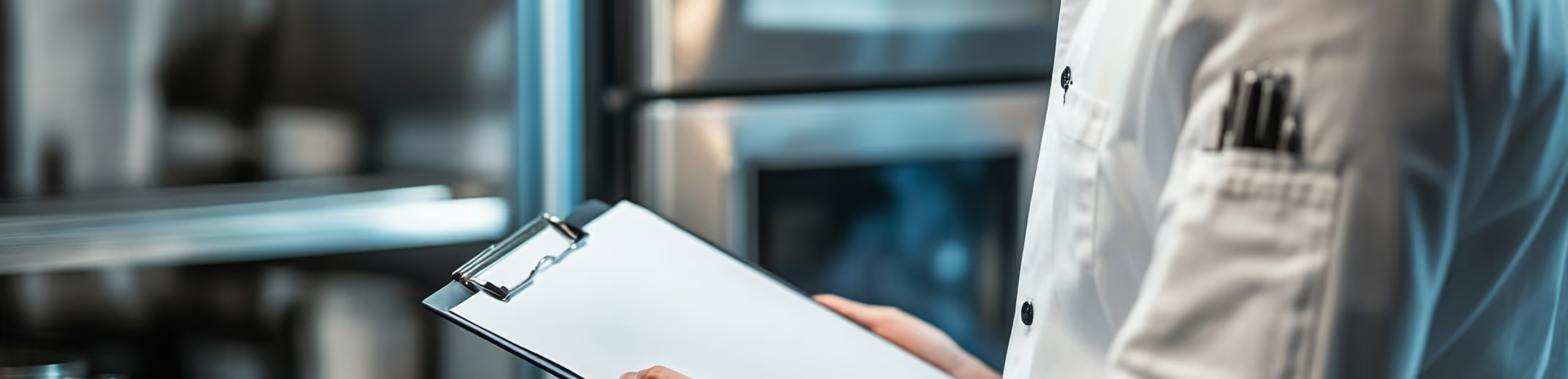